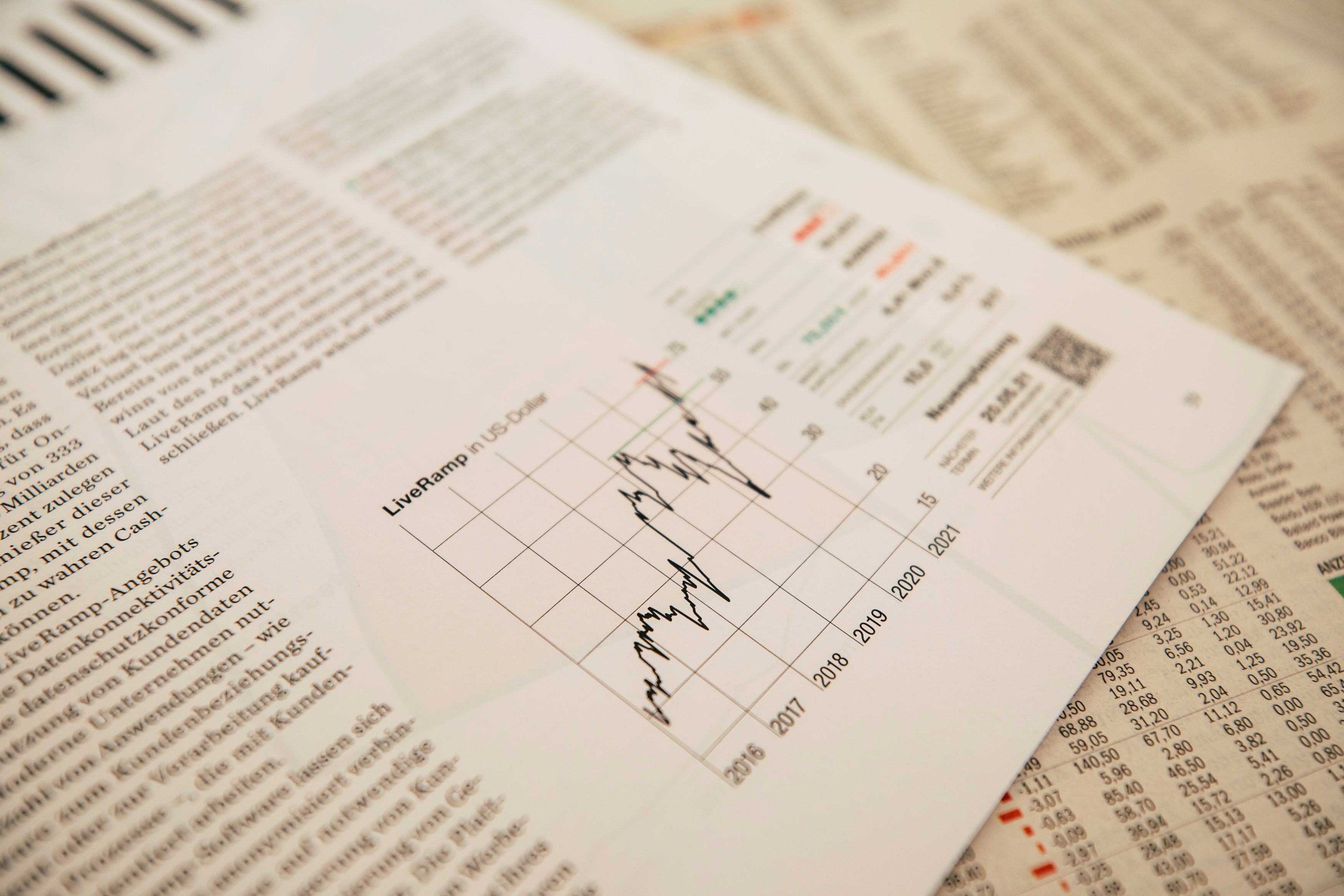
Blog / Reporting
Inventory Analysis
Sep 29, 2023
Inventory Analysis
Introduction
Inventory analysis is a crucial aspect of supply chain and financial management. It involves examining inventory levels, turnover rates, and the overall efficiency of inventory management processes. For CFOs and CEOs, understanding inventory analysis is essential for optimizing working capital, improving cash flow, and ensuring that resources are used efficiently. This article delves into the intricacies of inventory analysis, its importance, and the various methods and metrics used.
The Importance of Inventory Analysis
Inventory represents a significant investment for many companies. Whether it's raw materials, work-in-progress, or finished goods, inventory ties up capital and incurs holding costs. Analyzing inventory helps in:
Optimizing Cash Flow: Efficient inventory management can free up cash that can be used elsewhere in the business.
Reducing Holding Costs: By minimizing excess stock, companies can reduce storage, insurance, and obsolescence costs.
Improving Service Levels: Adequate inventory levels ensure that products are available when customers need them, leading to higher customer satisfaction.
Enhancing Operational Efficiency: Inventory analysis can identify bottlenecks and inefficiencies in the production process.
Key Metrics in Inventory Analysis
Inventory Turnover Ratio
This ratio measures how many times a company's inventory is sold and replaced over a specific period. A higher turnover indicates efficient inventory management, while a lower turnover might suggest overstocking or issues with product demand.
Formula:
Inventory Turnover Ratio = Cost of Goods Sold / Average Inventory
Days Sales of Inventory (DSI)
DSI indicates the average number of days it takes for inventory to be sold. A lower DSI is generally preferable, indicating faster inventory turnover.
DSI = (Average Inventory / Cost of Goods Sold) x Number of Days in Period
Gross Margin Return on Inventory Investment (GMROII)
This metric evaluates the profitability of inventory investments. It's especially useful for retailers and wholesalers.
GMROII = Gross Margin / Average Inventory Cost
Fill Rate
Fill rate measures the percentage of customer demand that is met through immediate stock availability, without backorders or stockouts.
Stock-to-Sales Ratio
This ratio compares the amount of inventory on hand to the number of sales made, often used in the retail industry.
Formula:
Stock-to-Sales Ratio = Beginning of Month Inventory / Sales for the Month
Advanced Inventory Analysis Techniques
ABC Analysis
This method categorizes inventory into three categories based on its importance:
A Items: High-value items with low sales frequency.
B Items: Moderate value and frequency.
C Items: Low-value items with high sales frequency.
By identifying these categories, companies can optimize inventory levels for each group, ensuring that high-value items are closely monitored.
Just-In-Time (JIT) Inventory
JIT is a strategy where inventory is ordered and received only when needed, reducing holding costs and waste. While it can improve efficiency, it requires accurate demand forecasting.
Economic Order Quantity (EOQ)
EOQ calculates the optimal order quantity that minimizes total inventory costs, including ordering and holding costs.
EOQ = Square Root of [(2 x Demand x Ordering Cost) / Holding Cost]
Safety Stock Analysis
Safety stock acts as a buffer against uncertainties in demand and supply. Analyzing and determining the right level of safety stock ensures product availability while minimizing excess inventory.
Challenges in Inventory Analysis
Demand Forecasting: Accurate demand forecasting is crucial for inventory analysis. Inaccuracies can lead to stockouts or overstocking.
Data Silos: For companies with multiple storage locations or complex supply chains, consolidating data can be challenging.
External Factors: Factors like geopolitical events, natural disasters, or global pandemics can disrupt supply chains, making inventory analysis more complex.
Conclusion
Inventory analysis is not just about counting stock. It's a strategic process that impacts a company's bottom line, operational efficiency, and customer satisfaction. For CFOs and CEOs, understanding and prioritizing inventory analysis can lead to significant cost savings, improved cash flow, and a competitive edge in the market.
Inventory Analysis
Introduction
Inventory analysis is a crucial aspect of supply chain and financial management. It involves examining inventory levels, turnover rates, and the overall efficiency of inventory management processes. For CFOs and CEOs, understanding inventory analysis is essential for optimizing working capital, improving cash flow, and ensuring that resources are used efficiently. This article delves into the intricacies of inventory analysis, its importance, and the various methods and metrics used.
The Importance of Inventory Analysis
Inventory represents a significant investment for many companies. Whether it's raw materials, work-in-progress, or finished goods, inventory ties up capital and incurs holding costs. Analyzing inventory helps in:
Optimizing Cash Flow: Efficient inventory management can free up cash that can be used elsewhere in the business.
Reducing Holding Costs: By minimizing excess stock, companies can reduce storage, insurance, and obsolescence costs.
Improving Service Levels: Adequate inventory levels ensure that products are available when customers need them, leading to higher customer satisfaction.
Enhancing Operational Efficiency: Inventory analysis can identify bottlenecks and inefficiencies in the production process.
Key Metrics in Inventory Analysis
Inventory Turnover Ratio
This ratio measures how many times a company's inventory is sold and replaced over a specific period. A higher turnover indicates efficient inventory management, while a lower turnover might suggest overstocking or issues with product demand.
Formula:
Inventory Turnover Ratio = Cost of Goods Sold / Average Inventory
Days Sales of Inventory (DSI)
DSI indicates the average number of days it takes for inventory to be sold. A lower DSI is generally preferable, indicating faster inventory turnover.
DSI = (Average Inventory / Cost of Goods Sold) x Number of Days in Period
Gross Margin Return on Inventory Investment (GMROII)
This metric evaluates the profitability of inventory investments. It's especially useful for retailers and wholesalers.
GMROII = Gross Margin / Average Inventory Cost
Fill Rate
Fill rate measures the percentage of customer demand that is met through immediate stock availability, without backorders or stockouts.
Stock-to-Sales Ratio
This ratio compares the amount of inventory on hand to the number of sales made, often used in the retail industry.
Formula:
Stock-to-Sales Ratio = Beginning of Month Inventory / Sales for the Month
Advanced Inventory Analysis Techniques
ABC Analysis
This method categorizes inventory into three categories based on its importance:
A Items: High-value items with low sales frequency.
B Items: Moderate value and frequency.
C Items: Low-value items with high sales frequency.
By identifying these categories, companies can optimize inventory levels for each group, ensuring that high-value items are closely monitored.
Just-In-Time (JIT) Inventory
JIT is a strategy where inventory is ordered and received only when needed, reducing holding costs and waste. While it can improve efficiency, it requires accurate demand forecasting.
Economic Order Quantity (EOQ)
EOQ calculates the optimal order quantity that minimizes total inventory costs, including ordering and holding costs.
EOQ = Square Root of [(2 x Demand x Ordering Cost) / Holding Cost]
Safety Stock Analysis
Safety stock acts as a buffer against uncertainties in demand and supply. Analyzing and determining the right level of safety stock ensures product availability while minimizing excess inventory.
Challenges in Inventory Analysis
Demand Forecasting: Accurate demand forecasting is crucial for inventory analysis. Inaccuracies can lead to stockouts or overstocking.
Data Silos: For companies with multiple storage locations or complex supply chains, consolidating data can be challenging.
External Factors: Factors like geopolitical events, natural disasters, or global pandemics can disrupt supply chains, making inventory analysis more complex.
Conclusion
Inventory analysis is not just about counting stock. It's a strategic process that impacts a company's bottom line, operational efficiency, and customer satisfaction. For CFOs and CEOs, understanding and prioritizing inventory analysis can lead to significant cost savings, improved cash flow, and a competitive edge in the market.